Die Wahl der Oberflächenbehandlung ist ein Problem, mit dem jeder Designer konfrontiert ist. Es stehen viele Arten von Oberflächenbehandlungsoptionen zur Verfügung, und ein hochrangiger Designer sollte nicht nur die Wirtschaft und die Praktikabilität des Designs berücksichtigen, sondern auch auf den Montageprozess und sogar den Umweltanforderungen achten. Im Folgenden finden Sie eine kurze Einführung in einige häufig verwendete Beschichtungen für Verbindungselemente, die auf den oben genannten Prinzipien basieren, als Referenz durch Verschlusspraktiker.
1. Elektrogalvanisierung
Zink ist die am häufigsten verwendete Beschichtung für kommerzielle Befestigungselemente. Der Preis ist relativ günstig und das Aussehen gut. Zu den allgemeinen Farben gehören schwarz und militärisches Grün. Die Antikorrosionsleistung ist jedoch durchschnittlich, und seine Antikorrosionsleistung ist die niedrigste bei den Zinkplattenschichten (Beschichtungsschichten). Im Allgemeinen wird der neutrale Salzspray -Test von verzinktem Stahl innerhalb von 72 Stunden durchgeführt, und spezielle Dichtungsmittel werden auch verwendet, um sicherzustellen, dass der neutrale Salzspray -Test mehr als 200 Stunden dauert. Der Preis ist jedoch teuer, was dem 5-8-fachen des normalen verzinkten Stahls beträgt.
Der Prozess der Elektrogalvanisierung ist anfällig für Wasserstoffverspräche, sodass die Schrauben oberhalb der Grad 10.9 im Allgemeinen nicht mit der Verbreitung behandelt werden. Obwohl Wasserstoff nach dem Verschleppen unter Verwendung eines Ofens entfernt werden kann, wird der Passivierungsfilm bei Temperaturen über 60 ° C beschädigt, so Dies hat eine schlechte Betriebsfähigkeit und hohe Verarbeitungskosten. In Wirklichkeit entfernen allgemeine Produktionsanlagen keinen aktiven Wasserstoff, es sei denn, sie werden von bestimmten Kunden vorgeschrieben.
Die Konsistenz zwischen Drehmoment und Voranziehkraft von verzinkten Verschlüssen ist schlecht und instabil und sie werden im Allgemeinen nicht zum Anschließen wichtiger Teile verwendet. Um die Konsistenz des Drehmomentvorladens zu verbessern, kann die Methode zur Beschichtung von Schmierstoffen nach dem Verpacken auch zur Verbesserung und Verbesserung der Konsistenz der Drehmomentvorspannung verwendet werden.
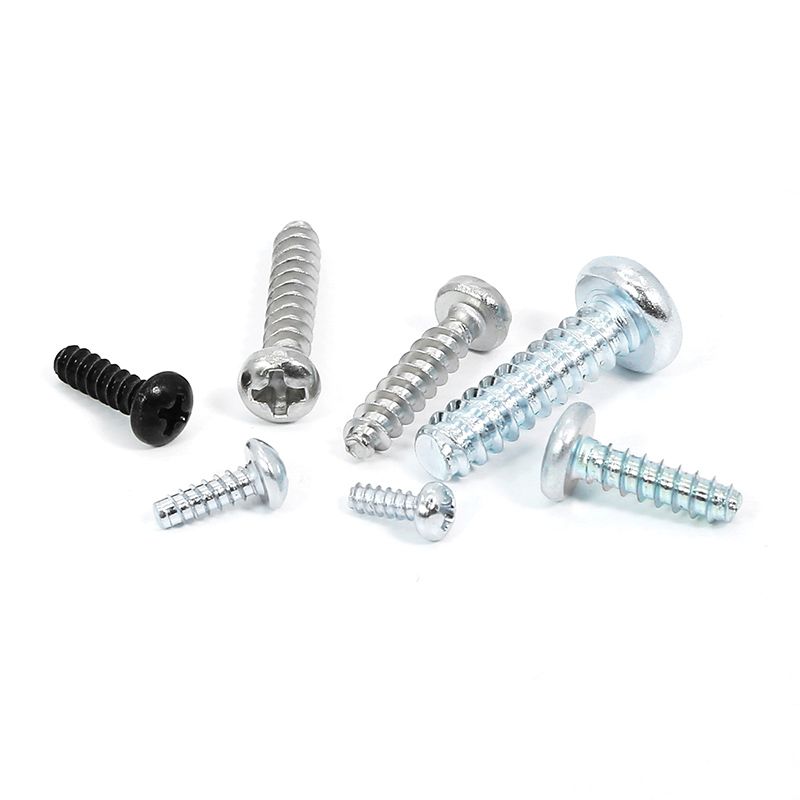
2. Phosphating
Ein grundlegendes Prinzip ist, dass Phosphating relativ billiger ist als die Galvanisierung, aber seine Korrosionsresistenz ist schlechter als die Galvanisierung. Nach der Phosphation sollte Öl angewendet werden, und seine Korrosionsbeständigkeit hängt eng mit der Leistung des angelegten Öls zusammen. Zum Beispiel nach Phosphating, auftragen ein allgemeines Anti-Rostöl und einen neutralen Salzspray-Test für nur 10-20 Stunden. Das Auftragen hochwertiger Anti-Rostöl kann bis zu 72-96 Stunden dauern. Sein Preis beträgt jedoch das 2-3-fache des allgemeinen Phosphatelöls.
Es gibt zwei häufig verwendete Phosphatetypen für Befestigungselemente, Phosphating auf Zinkbasis und Phosphating auf Manganbasis. Zinkbasierte Phosphating hat eine bessere Schmierleistung als Phosphating auf Manganbasis, und Phosphating auf Manganbasis weist eine bessere Korrosionsbeständigkeit und eine Verschleißresistenz auf als die Zinkplatte. Es kann bei Temperaturen von 225 bis 400 Grad Fahrenheit (107-204 ℃) verwendet werden. Insbesondere für die Verbindung einiger wichtiger Komponenten. Wie Stangenschrauben und Muttern des Motors, Zylinderkopf, Hauptlager, Schwungradschrauben, Radschrauben und Muttern usw.
Hochfestige Schrauben verwenden Phosphating, was auch Probleme mit Wasserstoffverspräche vermeiden kann. Daher verwenden Bolzen über der Klasse 10,9 im Industriefeld im Allgemeinen die Behandlung mit Phosphatebereich.
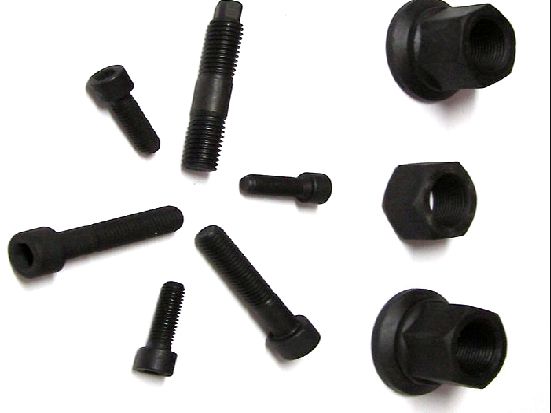
3. Oxidation (schwärzend)
Schwärzung+Ölen ist eine beliebte Beschichtung für Industriebefestigungen, da es am billigsten ist und vor dem Kraftstoffverbrauch gut aussieht. Aufgrund seiner schwärzenden Fähigkeiten hat es fast keine Rostpräventionsfähigkeit, so dass es ohne Öl schnell rostet. Selbst in Gegenwart von Öl kann der Salzspray-Test nur 3-5 Stunden dauern.
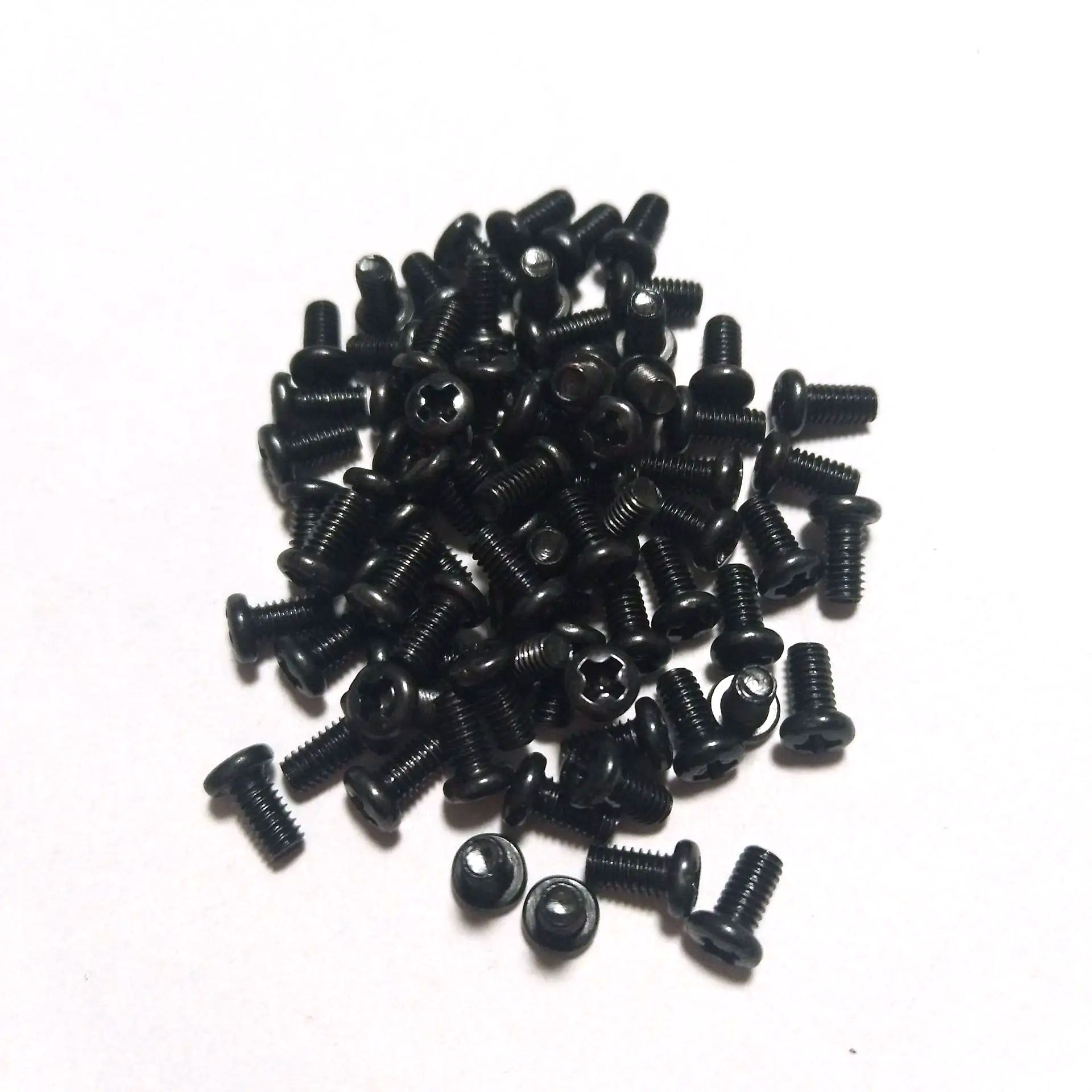
4. Elektroplatte Partition
Die Cadmiumbeschichtung weist im Vergleich zu anderen Oberflächenbehandlungen eine ausgezeichnete Korrosionsbeständigkeit auf, insbesondere in marinen atmosphärischen Umgebungen. Die Abfallflüssigkeitsbehandlungkosten bei der Elektroplatten von Cadmium sind hoch und der Preis beträgt das 15-20-fache des Elektroplatten von Zink. Daher wird es in allgemeinen Branchen nicht nur für bestimmte Umgebungen verwendet. Verbindungselemente für Ölbohrplattformen und HNA -Flugzeuge.
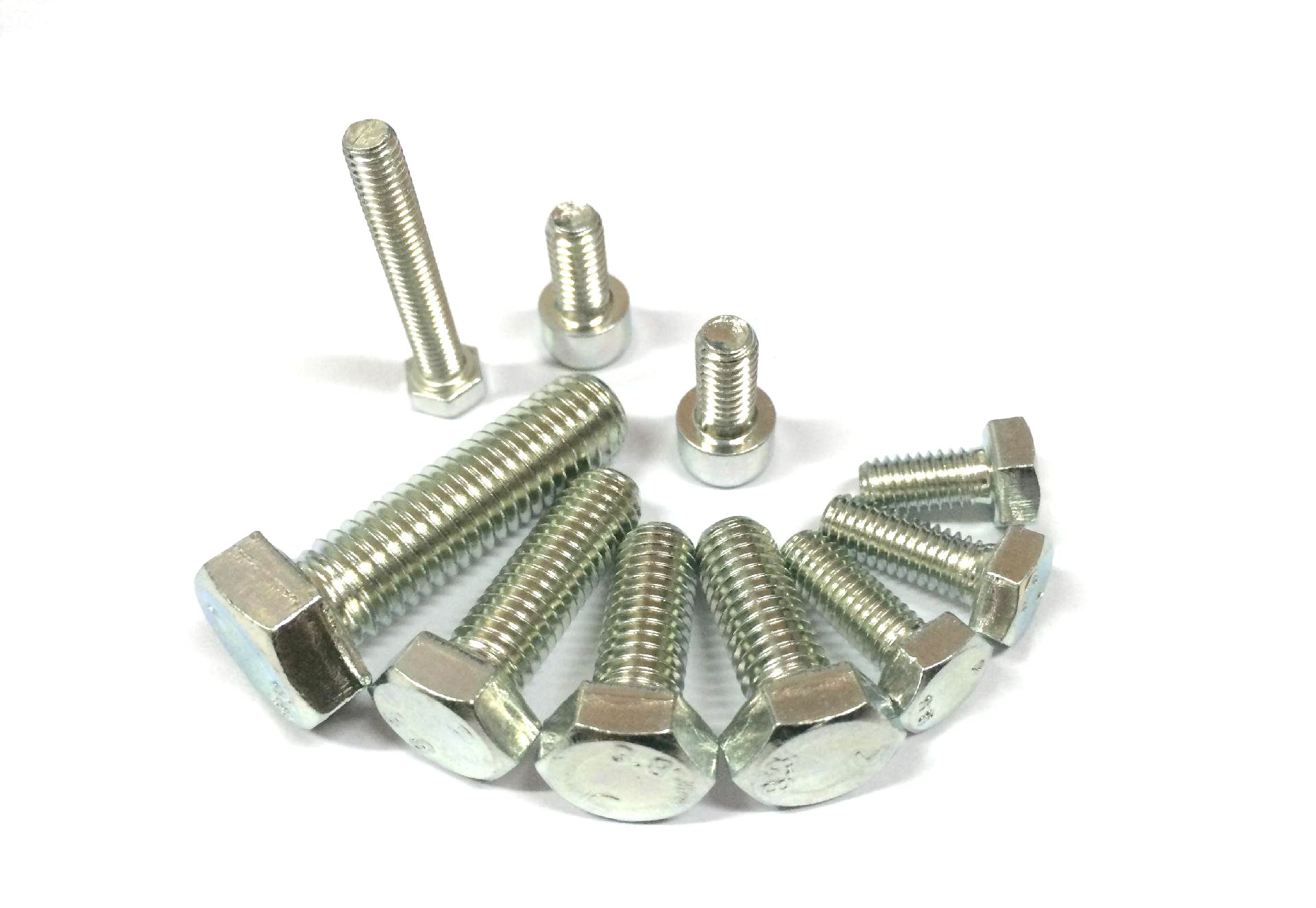
5. Chrombeschichtung
Die Chrombeschichtung ist in der Atmosphäre sehr stabil, nicht leicht zu ändern und Glanz zu verlieren und hat eine hohe Härte und eine gute Verschleißfestigkeit. Die Verwendung von Chrombeschichtung an Befestigungselementen wird im Allgemeinen für dekorative Zwecke verwendet. Es wird selten in Industriefeldern mit hohen Korrosionsbeständigkeitsanforderungen verwendet, da gute verchromte Verschlüsse wie Edelstahl gleichermaßen teuer sind. Nur wenn die Stärke der rostfreien Stahl nicht ausreicht, werden stattdessen verchromte Verschlüsse verwendet.
Um Korrosion zu verhindern, sollten Kupfer und Nickel zuerst vor der Chrombeschichtung plattiert werden. Die Chrombeschichtung kann hohen Temperaturen von 1200 Grad Fahrenheit (650 ℃) standhalten. Es gibt aber auch ein Problem der Wasserstoffverspräche, ähnlich wie bei Elektrogalvanisierung.
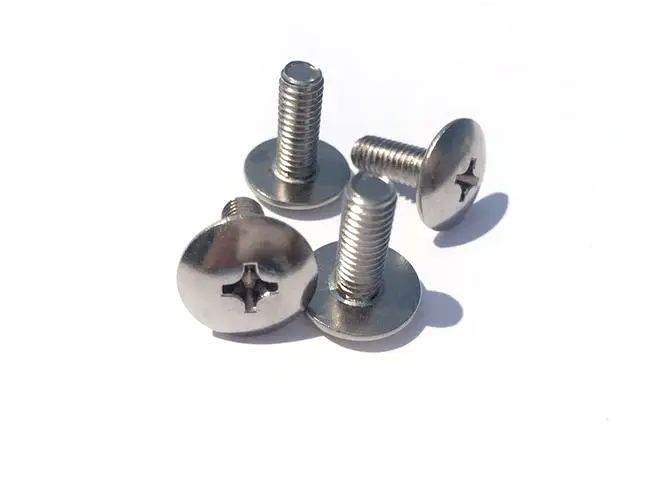
6. Nickelbeschichtung
Hauptsächlich in Bereichen, die sowohl Antikorrosion als auch gute Leitfähigkeit erfordern. Zum Beispiel die ausgehenden Terminals von Fahrzeugbatterien.
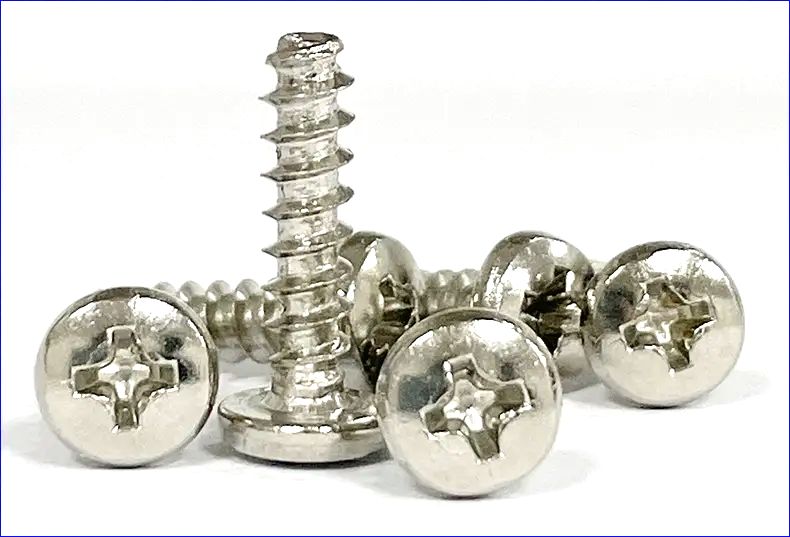
7. Heißtip-Galvanisierung
Heißes Dip -Galvanisierung ist eine thermische Diffusionsbeschichtung von Zink, die auf eine Flüssigkeit erhitzt wird. Die Beschichtungsdicke liegt zwischen 15 und 100 μm. Und es ist nicht einfach zu kontrollieren, hat aber einen guten Korrosionsbeständigkeit und wird häufig in der Technik verwendet. Während des Gasprozesses mit heißem Dip -Galvanisierung kommt es zu einer starken Verschmutzung, einschließlich Zinkabfällen und Zinkdampf.
Aufgrund der dicken Beschichtung hat es Schwierigkeiten beim Verschrauben in inneren und externen Gewinnen in Befestigungselementen verursacht. Aufgrund der Temperatur der Heißtip-Galvanisierungsverarbeitung kann sie nicht für Befestigungselemente über der Klasse 10,9 (340 ~ 500 ℃) verwendet werden.
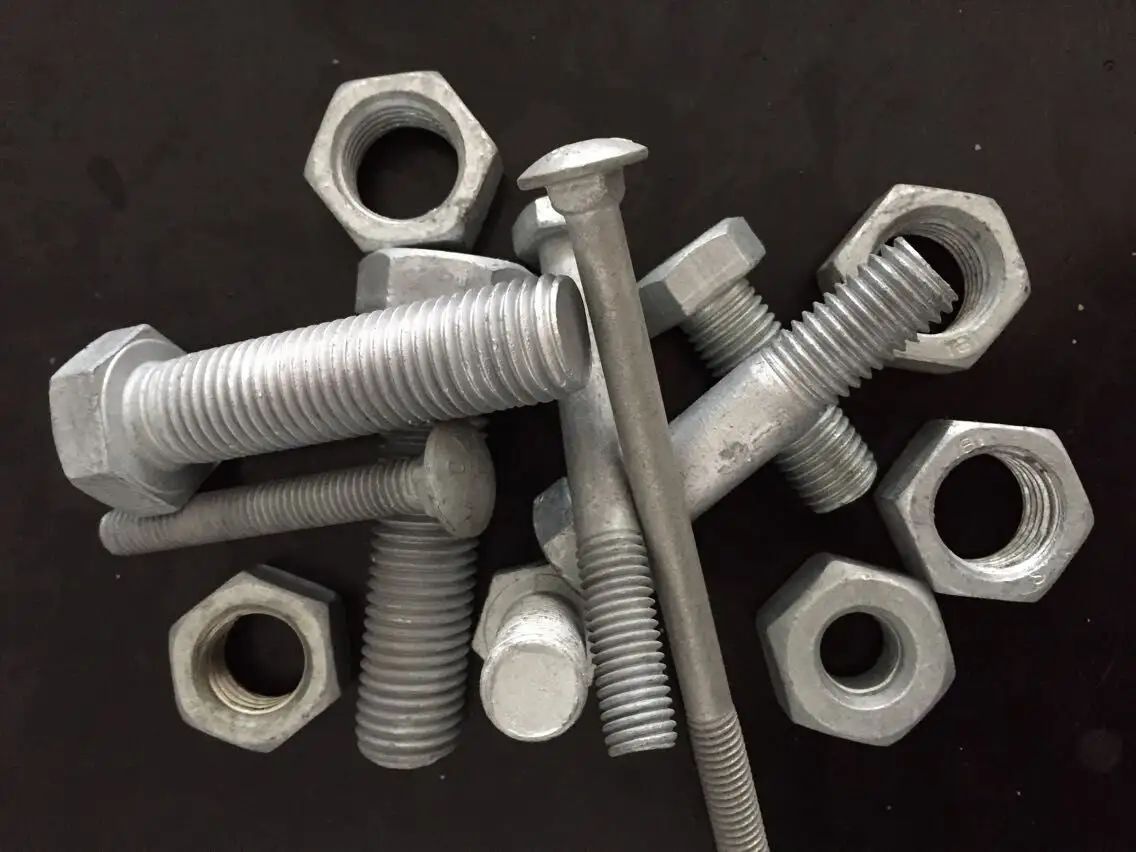
8. Zinkinfiltration
Die Zinkinfiltration ist eine metallurgische thermische Diffusionsbeschichtung von Zinkpulver. Seine Einheitlichkeit ist gut und eine gleichmäßige Schicht kann sowohl in Fäden als auch in Blindlöchern erhalten werden. Die Plattierungsdicke beträgt 10-110 μm. Und der Fehler kann bei 10%gesteuert werden. Seine Bindungsstärke und die Antikorrosionsleistung mit dem Substrat sind die besten in Zinkbeschichtungen (wie Elektrogalvanisierung, Heißtip-Galvanisierung und Dacromet). Der Verarbeitungsprozess ist umweltfreundlich und am umweltfreundlichsten.
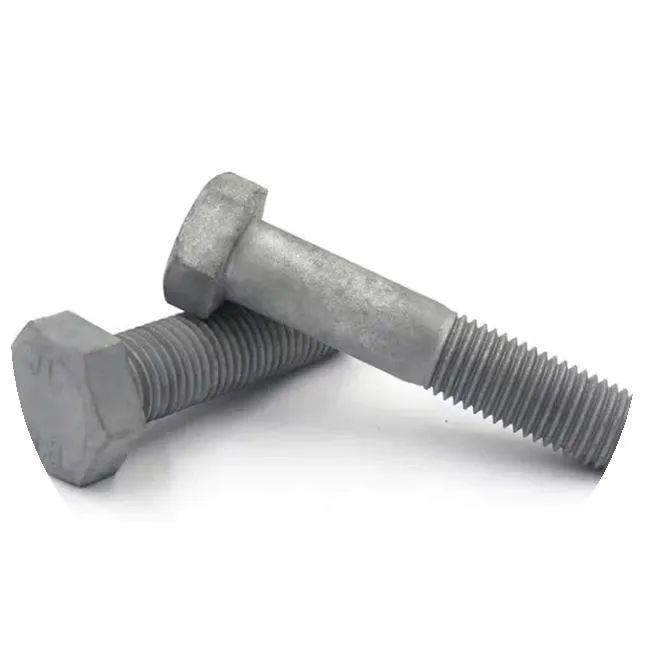
9. Dacromet
Es gibt kein Problem mit Wasserstoff -Verspritzung, und die Drehmoment -Vorspannungskonsistenzleistung ist sehr gut. Dacromet ist ohne Berücksichtigung von Chrom- und Umweltproblemen tatsächlich am besten für hochfeste Befestigungselemente mit hohen Korrosionsanforderungen geeignet.
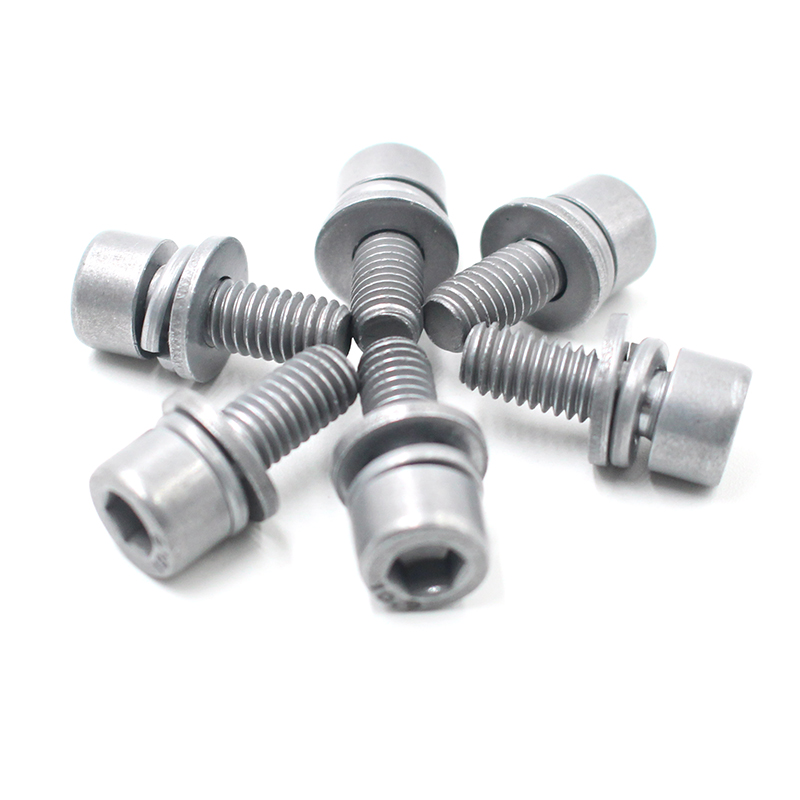
Postzeit: Mai 19. bis 2023